为解决传统门机在人工操作模式下存在的智能化、信息化水平低、劳动强度大等一系列问题,研发基于多维感知和智能控制的全自动门机,以门机自动化控制系统为核心,以港机装备全生命周期管理平台为数据中台,以智能安全防护系统、智能振温监测系统、智能作业统计系统、智能势能回收系统、智能风力预警系统、基础电气控制系统为基础功能模块,实现3个基础层的相互融合、相互通信,形成一种具有智能控制、多维感知、本质安全的全自动化门机。
目前,国内外港口的门机主要采用人工操作进行散货装卸作业,门机的作业范围以及各机构运动均由司机通过操作台控制。门机现有操作方式存在以下问题:一是传统的作业方式完全依靠门机司机进行操控,对司机操作技能要求高,司机劳动强度大;二是作业效率完全依赖司机的技能水平,平均作业效率不能保证;三是门机作业工况较为复杂,人工疲劳操作、视野受限等因素导致港口各类碰撞等安全事故频发。
利用实时激光扫描技术建立船体、物料、岸上设施的空间三维模型,结合对各机构位姿信息的精确检测,并攻克抓斗防摇、抓斗运行轨迹优化、作业自动规划、空间防碰撞等技术,最终实现门机全自动操作。
基于多维感知和智能控制的全自动门机解决方案以门机自动化控制系统为核心,以港机装备全生命周期管理平台为数据中台,以门机多维感知系统核心技术为基础功能模块,实现门机作业自动化与智慧运维双效合一的现代化港口用门机。基于多维感知和智能控制的全自动门机架构见图1。
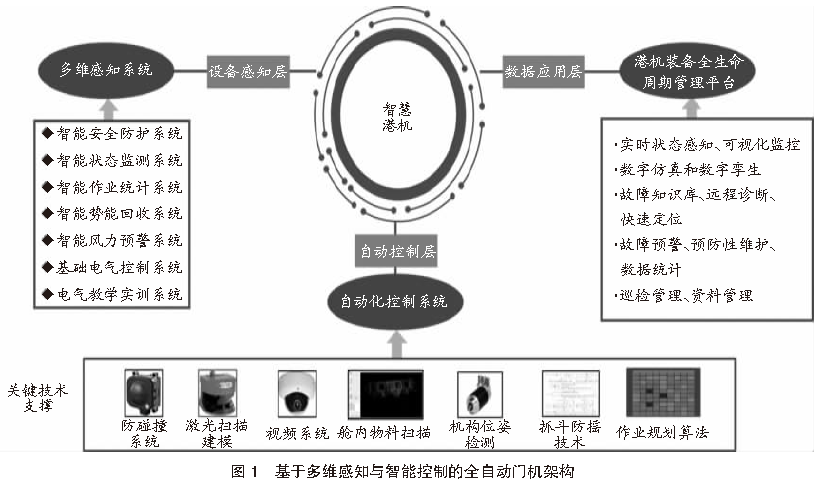
门机自动化控制系统。通过实时激光扫描技术建立船体、物料、岸上设施的空间三维模型,实现对各机构位姿信息的精确检测,并攻克抓斗防摇、抓斗运行轨迹优化、作业自动规划、空间防碰撞等技术,最终实现门机全自动作业和智能远程控制。
港机装备全生命周期管理平台。采用数字孪生、物联网、建模分析等技术,通过数据感知、数据传输、数据应用等3层结构,打造具有状态实时监控、故障诊断、预防性维护、健康分析、数据展示为一体的管理信息化平台。
多维感知系统。融合绝对值编码器、毫米波雷达、振动传感器、风速风向传感器、2D/3D激光扫描仪、视觉图像等设备,构建门机智能安全防护系统、智能状态监测系统、智能势能回收系统、智能风力预警系统等子系统,在中控室集中控制系统的统一协调控制下,实现整机的智能化控制。
2.1 门机自动化控制系统
以核心关键技术为支撑,构建自动控制底层架构,通过上位机智能算法,对门机各运行动作自动规划、控制,实现全程自动化作业。
2.1.1 机构位姿检测技术
利用编码器等装置实时反馈各个机构的位姿状态信息,并通过误差建模和标定方法实现对门机系统的几何参数和刚度参数的辨识和补偿,使系统能够实时精确地获得变负载情况下的门机机构的运动轨迹和位姿信息。
2.1.2 激光扫描建模技术
利用冗余激光云台扫描设备实现目标区域的精确识别,同时从机械结构和多传感器数据融合等2个方面降低振动对于测量精度的影响,能够实现船体、船舶舱口位置、船舷高度、船舱盖板、物料堆型、装卸位置等目标区域的扫描建模。
2.1.3 抓斗防摇技术
根据起升钢丝绳等效绳长等数据,结合各机构速度,估算出偏摆角度。通过建模分析出角度衰减控制情况,实现抓斗防摇。
2.1.4 防撞检测技术
依托各机构的精准定位和位姿获取,通过软件算法计算本机与相邻流程设备的运动趋势,实现软件防撞功能。
2.1.5 抓斗运行轨迹优化
通过建立抓斗的运动模型和力学分析模型,根据轨迹规划曲线的起止点处的2个期望点的位置和速度参数关系及加速度和加加速度来限制升降速控制曲线,实现抓斗轨迹最优控制。
2.1.6 数据通信技术
打通门机中心滑环和电缆卷盘滑环等2个节点,采用光纤滑环实现机上与机下、门机与中控的光纤通信。
2.1.7 作业规划算法
通过激光扫描建立船舱物料模型,系统根据规划算法自动选择抓斗最佳抓取点。
2.1.8 机群协同自动作业
通过远程控制系统,建立各流程设备之间的主从控制,即从控制门机模仿主控制门机的机构动作和抓斗运行轨迹,实现1名司机操作多台门机。
2.2 门机多维感知系统关键技术
智能安全防护系统。整机自动防撞。
智能状态监测系统。关键部位的振动、温度在线监测和诊断、故障预警、故障诊断。
智能势能回收系统。起重机吊重下降势能回收转化为电能储存并释放用于电机驱动,节能减排。
智能风力预警系统。风速精确监测、报警,提升港口大型起重机械防风防台能力,提高港口装卸作业效率和保障装卸过程安全。
基础电气控制系统。变频器技术实现不同设备、不同机构的运行速度控制和调节,PLC技术实现各个机构电气逻辑流程控制。
2.3 全生命周期智慧运维监管平台
采用数字孪生、物联网、建模分析、传感器、5G通信等技术整合门机的基础控制系统、振动温度、作业统计、环境信息、能源、视频等系统底层数据,通过数据感知、数据传输、数据应用等3层结构,打造具有远程实时监控、故障诊断、预防性维护、健康评估、数据展示和分析功能的港机装备全生命周期智慧运维监管平台。
3.1 全自动控制系统门机
通过实时激光扫描技术建立船体、物料、岸上设施的空间三维模型,结合对各机构位姿信息的精确检测,攻克抓斗防摇、抓斗运行轨迹优化、作业自动规划、空间防碰撞等技术,实现门机全自动作业和智能远程控制。全自动门机具备下列主要特征:
3.1.1 抓斗防摇
利用非均匀有理B样条曲线(NURBS曲线)进行门机作业任务的轨迹规划,可以得到连续且各关节无速度、加速度突变的轨迹曲线。由于NURBS曲线具有局部修改性,移动控制顶点、调整节点矢量或改变权因子仅影响NURBS曲线的局部形状,不会影响整体轨迹的性能。采用笛卡尔空间的控制点数据对空间自由曲线轮廓进行描述,同时采用阿当姆斯微分方程进行NURBS插补密化计算,并以最大轮廓误差、最大加速度为约束条件自适应调整插补速度,继而将插补所得短直线段采用倍四元数将笛卡儿空间中的门机位置和姿态转换至四维空间,用超球面旋转对门机的运动轨迹进行球面线性插补,最终实现门机NURBS自由曲线轨迹规划。在此基础上,在门机自动运行过程中,根据抓斗摆动幅度获取等效摆长信息,所述等效摆长信息为抓斗在最高位置时进行摆动运动对应的长度值;根据等效摆长信息生成平均摆动周期;根据平均摆动周期生成速度理论曲线;根据速度理论曲线获取第1减速点信息和第2减速点信息;计算平均摆动周期与第2减速点信息之间的差值并将所述差值设置为减速时间信息;控制第1减速时间点信息和减速时间信息对应的时间值相同,抓斗在运动过程中分为加速、匀速和减速等3种形式的运动,其中在加速和减速经历的时间相同时,抓斗的防摇效果最好,抓斗在运行过程中减少晃动幅度,从而有效抑制门机抓斗的摆动。
3.1.2 抓斗运行轨迹优化
当门机在最大幅度时,抓斗位于船体的水平中线附近,为了抓取最远端的物料,抓斗需要在保证安全操作的前提下实现舱内自动抛斗,因此需要对抓斗运行轨迹进行优化。首先,通过建立抓斗的运动模型和力学分析模型,根据三角函数的位置、速度、加速度和加加速度的模型,确定轨迹规划曲线起止点处的2个期望点的位置和速度参数。其次,将边界条件的参数值代入所建立的模型中,列出方程组并求出模型的参数。最后,根据轨迹规划曲线起止点处的2个期望点的位置和速度参数关系及加速度和加加速度来限制升降速控制曲线,确定期望的规划轨迹,实现抓斗轨迹最优控制,在抓斗下降到舱内固定高度时,利用变幅运动将抓斗抛到舱内预定位置,进行取料作业。
3.1.3 作业自动规划
抓斗在抓取作业过程中,利用起升机构调节抓斗的高度,利用回转机构调整抓斗相对于回转机构中心点的角度,利用变幅机构来调节抓斗距离回转机构中心点之间的距离,此时抓斗距离回转机构中心点之间的水平距离信息即为变幅机构的幅度变化量信息。根据变幅机构的幅度变化量和回转机构转动的回转角度来确定抓斗相对于回转机构中心点的水平相对位置信息,再根据水平相对位置信息和抓斗相对于回转机构中心点的高度来确定抓斗相对于回转机构中心点的实际位置,进而实现对抓斗的自动定位。激光云台扫描设备采用激光雷达携带云台的方式对目标区域进行数据采集生成点云图,结合相关算法对原数据进行降噪处理,结合所需识别目标的特征结构,在降噪后的数据中匹配特征点,通过特征点划定出目标物体在激光视角中的空间中的位置,结合空间坐标转换,将激光视角下的空间坐标系转化为实际大地物料坐标系,以达到准确定位舱口、船舷甲板、物料区域等特征目标的实际物理坐标位置。按照预设的图片划分规则,将物料区域点云图划分为若干物料区域图,计算所有物料区域图的平均点云高度,并筛选出所有物料区域图中的点云高度最高值所对应的物料区域,将点云高度最高值所对应的物料区域设置为抓斗的作业点,控制抓斗按照预设的抓取路线进行作业。
3.1.4 空间防碰撞
在装卸设备相应位置安装激光雷达,直接监控视场范围内的障碍物情况,后台算法只需计算本机与相邻流程设备的运动趋势,判断是否存在碰撞的可能,并进行相应处理,实施防碰撞措施。这种方式使传感器的选择、布置更加灵活,可根据实际需求动态调整监控区域,从而最大程度保证系统安全运行。本机位置可通过锚定装置确定,姿态通过编码器、雷达、视觉等装置进行检测。
3.2 起重装备多维感知子系统
通过编码器、雷达、振动传感器、风速风向传感器、激光扫描、视觉图像等方法采集原始数据,融合门机位姿和作业环境的精确信息,构建港机装备智能安全防护系统、智能状态监测系统、智能势能回收系统和智能风力预警系统等子系统,在中控室集中控制系统的统一协调控制下,实现整机的智能化控制。
3.2.1 门机机构的高精度位姿检测技术
门机系统的全自动化需要实时监控各个机构运动轨迹和位姿信息。在系统驱动部件上安装高精度编码器实现机构位姿的精确计算。但由于门机系统的机械结构在加工和组装过程中存在一定误差,在基于编码器计算位姿时存在一定误差。
为进一步提升轨迹和位姿检测精度,利用高精度激光跟踪仪对门机系统中机构运动轨迹和位姿进行精确测量。首先,利用DH建模方法构件门机系统的运动学模型,并且分析各个几何参数对于门机系统的精度影响。其次,构建门机系统的刚度模型,分析不同负载下门机系统刚度误差,确定影响门机系统精度的刚度参数。最后,通过参数误差补偿,实现门机系统运动轨迹、位姿的精确补偿。
3.2.2 基于多传感器融合的三维扫描建模技术
为实现船舶舱口位置、船舷高度、物料、装卸位置的精确识别,在门机系统的象鼻梁端部安装2台激光云台扫描设备。通过云台动态控制激光雷达扫描俯仰角度范围,扫描区域可覆盖作业区域,保证了对识别目标数据采集的完整性;利用冗余的激光云台扫描设备进行数据融合,提升三维信息的检测精度。
门机系统的振动对激光云台扫描精度的影响较大,为消除振动影响因素,创新性地从多传感器数据融合和机械结构设计等2个方面解决该问题。一是通过云台配置阻尼和重锤,从机械结构上降低振动对于激光扫描数据的影响;二是通过云台配置惯性测量单元和视觉检测传感器,实时反馈激光云台扫描设备的姿态。
3.2.3 非稳态负载下的振动监测分析方法
获取起升机构非稳态负载下实时转速,实时转速为起升机构电机在实际运行中的实时转速值。判断实时转速是否大于预设的临界转速,若实时转速不小于预设的临界转速,则获取振动波形信息以及对应振动波形信息的异常转速。根据振动波形信息计算对应的相关特征值信息,将相关特征值信息与预设的故障分析库中的故障分析频率进行比对,预设的故障分析库中储存有不同的故障分析结果以及与故障分析结果相对应的故障分析频率,若相关特征值与故障分析频率相同,则发送与故障分析频率相对应的故障分析结果至工作人员的智能终端,实现对非稳态负载下振动的检测分析。
3.3 全生命周期智慧运维监管平台
采用数据感知、数据传输、数据应用等3层结构,打造具有远程实时监控、故障诊断、预防性维护、健康评估、数据展示和分析功能的全生命周期智慧运维监管平台,提升精细化管理水平,实现“一对多”的控制室远程智能监管,提高港口生产作业的自动化、智能化水平。全生命周期智慧运维监管平台主要由6个子系统构成。
3.3.1 数字孪生子系统
利用BIM、三维引擎、大数据分析等技术,进行三维场景建模,还原港机设备三维实体,对设备全要素整体还原,与港机设备相关业务对接,实现港机设备运行状态与三维模型实时动态联动。
3.3.2 起重设备监视子系统
基于每台设备内容管理系统(CMS)内已有的PLC硬件设备,通过无线或有线连接的方式,实现每台港机设备本地CMS中PLC与港机装备全生命周期管理平台的互联互通。
3.3.3 振温监测子系统
基于振动监测系统已有的后台数据,利用已有的各级数字数据网(DDN)专网、无线通信等,通过系统对接的方式,实现振动监测系统与全生命周期管理平台的数据互联互通,从而获取港机设备重要部位的振动信息数据、温度信息、故障信息等。
3.3.4 超负荷监控子系统
基于门机称重系统内已有的PLC硬件设备,通过无线或有线连接的方式,实现每台门机本地超负荷系统中PLC与全生命周期管理平台的互联互通。
3.3.5 能源管理子系统
通过在港区大型港机设备的配电柜内配置多功能电力仪表,实现对电能数据的采集,通过在现有PLC计算上配置远程终端单元,实现多功能电力仪表采集数据远程传输至港机装备全生命周期管理平台。
3.3.6 视频监控子系统
利用已有的各级DDN专网,实现各港区视频监控系统与港机装备全生命周期管理平台的互联互通,轻松直观地进行调度监看、联动监控,及时识别安全隐患,预防事故发生,保障港口各项业务安全、快速运转。
目前,基于多维感知与智能控制的全自动门机已在南京港集团新生圩港务分公司和泰州过船港务有限公司码头安装调试完成,并交付用户使用,经运行测试,各项参数达到目标要求。半自动作业流程已实现抓斗闭斗抓料、移至料斗上方卸料、回到抓料点整个过程的自动运行;全自动作业流程已实现整个作业流程自动循环运行,无需人工干预,自动化作业效率达到平均人工作业效率的95%,自动化作业率达到85%~90%,远程操作可实现1名司机同时控制2台门机作业。
设备连续稳定运行提供有力保障。